MyMeter monitors the building throughout its life: every day starting with the installation of the structures on site.
We are the story of your wooden house!
Paolo Marchetto - Technical manager
Many people what is the best time to install the MyMeter System. The answer is as simple as the question: as soon as possible.
Since wooden structures can accumulate high quantities of humidity already in the transport phases and then on-site, it is important to start monitoring their concentration as soon as possible.
In fact, more and more frequently there are problems of durability due to humidity accumulated by the structures during the construction phase. This phenomenon is much more frequent in public procurement, where the construction times can be extended more frequently, multiplying the risk of criticality for the wood.
Also for this reason it is advisable to activate the wood moisture monitoring as soon as the structures have been installed.
Furthermore, in the event of delays in construction site operations, suitable rainproof protection must be provided for all wooden portions.
The "closure" of the structures
Very often, when the MyMeter System is started up after the building is completed, very high humidity values are detected, sometimes exceeding the safety limits.
How can this happen?
It is very common, in fact, that when the wooden structure is "closed" - the ETICS and the internal counter wall are created -, the humidity level of the wood reaches critical levels, which would discourage the closure itself.
To correctly evaluate when to close, it is essential to have reliable data relating to the humidity of the wood and to evaluate its "tendency" to dry.
To allow the monitoring of the wood also in this phase, MyMeter can be a valid ally by adopting two different procedures
- temporary activation of MyMeter: after installing all the probes in the pre-established points, the MySenseRadio sensors and the MyCPU 100 control unit, housed in temporary IP56 electrical boxes, are activated and the monitoring activity begins already during the construction phases. Subsequently, if the project involves the use of radio sensors, these will be removed from the IP 56 boxes and housed in the plasterboard. If the definitive project envisages the MySenseBus wired sensors, the radio sensors will be removed, they will be replaced by the radio ones and the wiring between sensors and control units will be made.
- manual detection: it consists in inserting the probes in the predetermined points and using them as electrodes for measuring the humidity values through portable hygrometers. This completely manual operation requires keeping track of the measured values. The wiring of the sensors and the installation of the control unit will be done at a later time. At the end of the installation the system will be activated
From now on, MyMeter will monitor the building for its entire life, becoming a trusted monitoring tool. At any time the data will be controllable from smartphone, tablet or PC, through a dedicated account.
Furthermore, if requested by the owner, the data will also be available to the constructor and the designer.
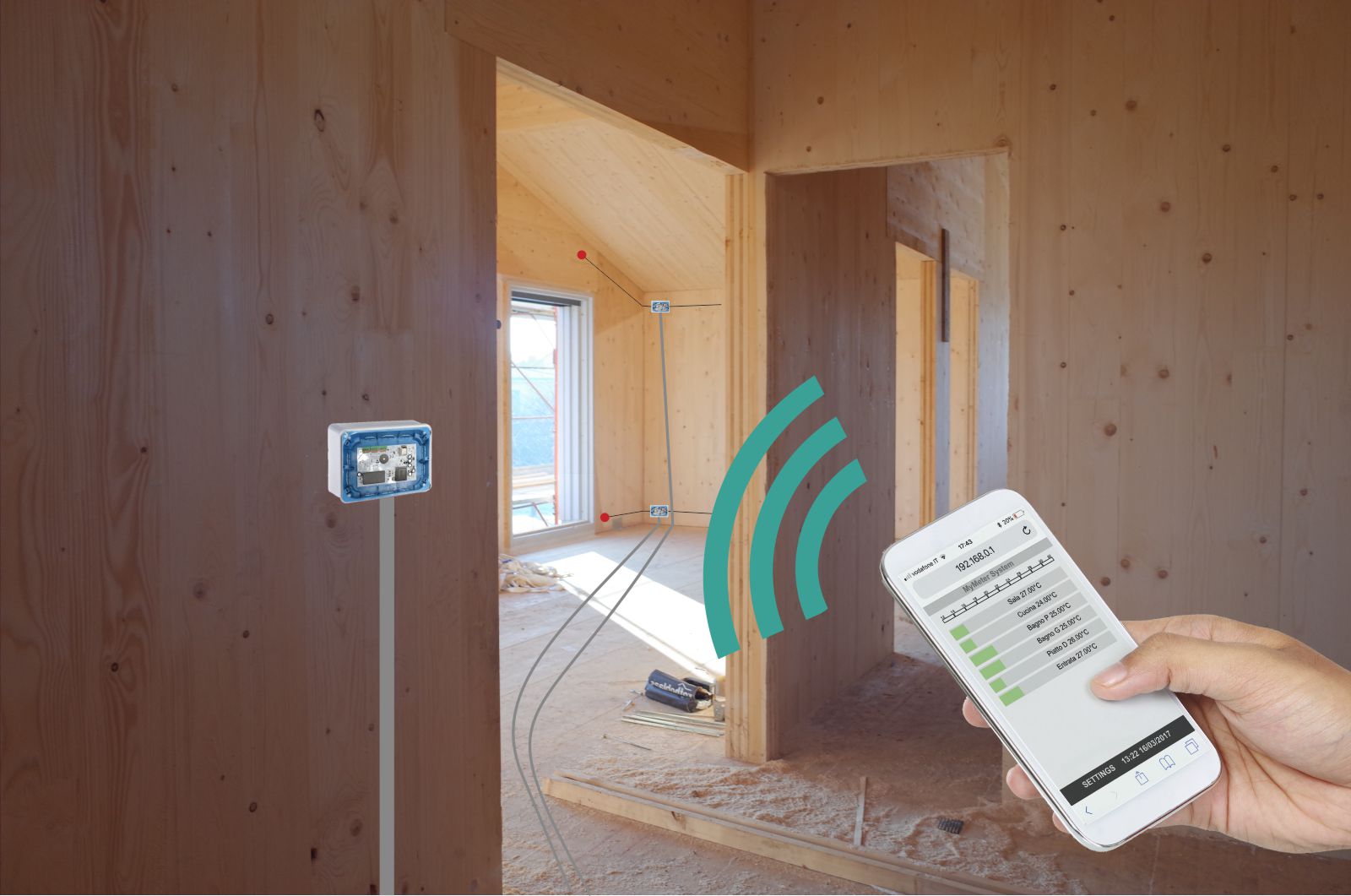
Post remediation monitoring
MyMeter is also widely used as a monitoring system to verify the effectiveness of repairs to wooden structures that have had humidity problems.
Following humidity problems, which often lead to legal disputes, once the restoration and safety operations have been carried out, MyMeter is installed to monitor the effectiveness of the intervention carried out.
If the repair has been carried out correctly, the sensors will show lower and lower humidity values and a constant trend to progressively decrease.
Also for this use, the longer length probes of MyMeter allow the monitoring of humidity along the entire thickness of the wood and of each layer of CLT.
Do you want to know more?
Download the application brochure and contact us for more information